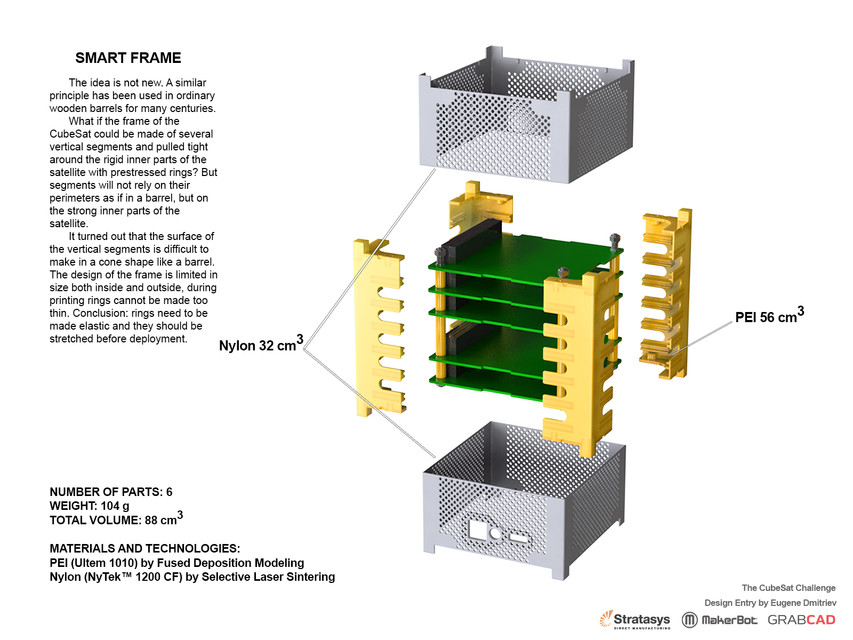
CubeSat Smart Frame
grabcad
This challenge entry presents a unique solution to fulfill the four conflicting requirements for the CubeSat structure design. The frame is designed using several vertical segments, which are pulled tight around the rigid inner parts by prestressed rings. The base of the structure consists of corner pieces made from polyetherimide (Ultem 1010), providing durability and resistance to thermal and radiation impact. These corner pieces embrace the inner PCBs with mounting seats. The outer rectangular rings, made from nylon, are placed on both sides alongside the Z-axis of the Supporting Units after preheating or mechanical tension. This design provides a thermal (shrink) fit, which is preferable for assembly. The internal structure along the Z-axis can be variable to modulate tension forces in specific areas. Nylon was chosen due to its elasticity, high thermal resistance, and relatively low cost. PEI was selected for the corner pieces due to its high strength, heat and frost resistance, radiation resistance, and commercial availability. Special tools and fixtures may be necessary for assembly but can also be produced using additive manufacturing techniques. The space between the boards can be filled with a thermally conductive and radiation-resistant material for improved heat dissipation.
With this file you will be able to print CubeSat Smart Frame with your 3D printer. Click on the button and save the file on your computer to work, edit or customize your design. You can also find more 3D designs for printers on CubeSat Smart Frame.