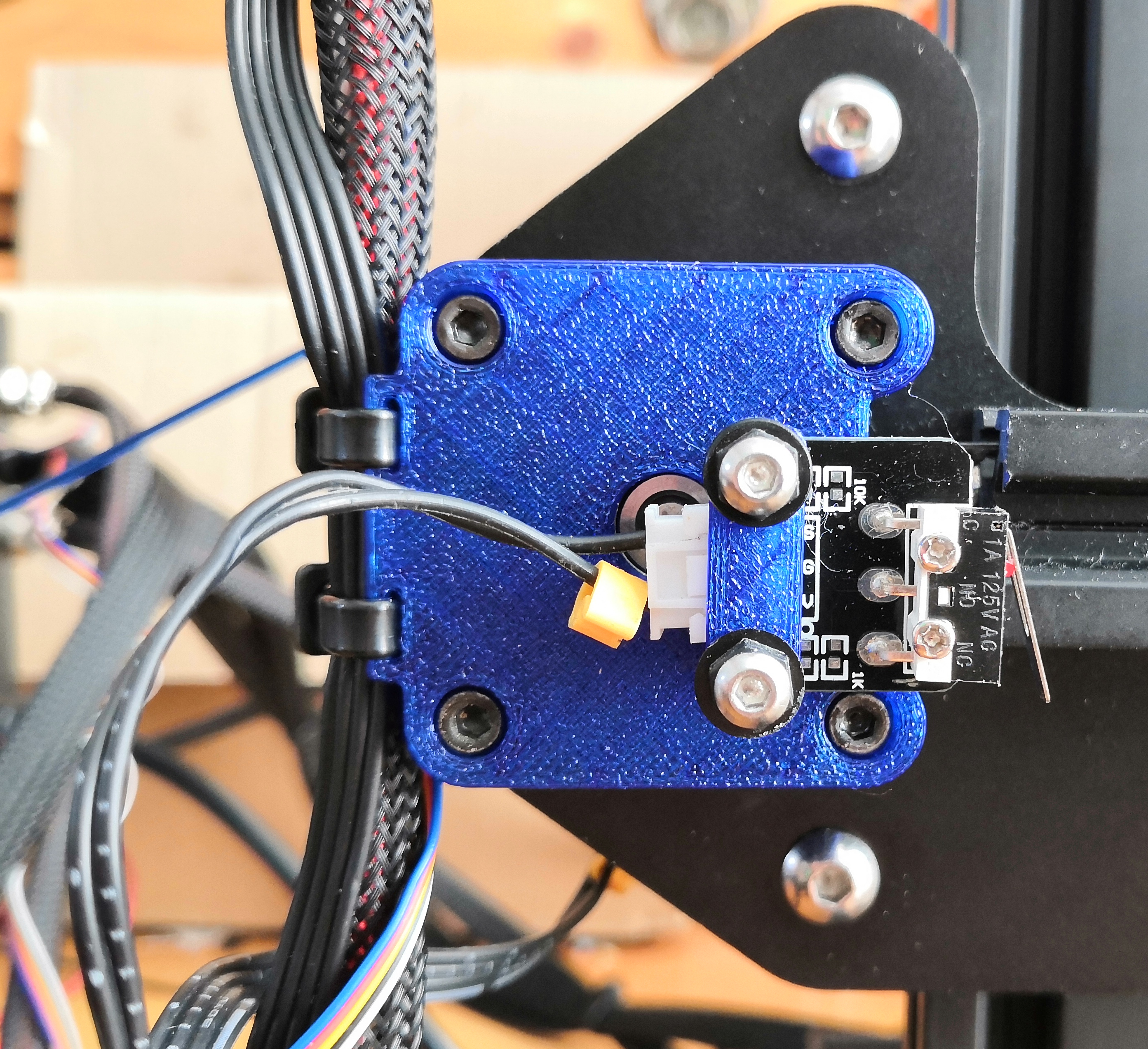
Creality CR-10 X and Y axis stepper shaft reinforcing counter bearing housings (probably fit Ender-3 too)
prusaprinters
<h3>Problem</h3><p>The X and Y stepper mounts on the CR-10 tend to flex when under higher load and using enough belt tension to be able to use higher acceleration values. I initially tried to use a stiffer mount plate, but that did not solve the issue, rather, now the stepper shaft flexed, which is definitely worse. </p><p>The amount of deflection is small in both cases, but it's enough so the pulley does not sit parallel to the belt anymore. This creates unnecessary load/friction - meaning wasted energy, resulting in less effectively available torque to actually move the X and Y carriages and lower attainable speeds and accelerations. In effect, the steppers stall/skip steps earlier than they would without the added friction. Since my CR-10 is an old model, it only runs 12V and does not have too much headroom anyway, considering it has a 300x300mm bed to move as well as a DD extruder.</p><h3><TL;DR></h3><p>Make printer go brrrrrrrrrr not squeak pop taktaktak :D</p><h3>Solution</h3><p>Design a counter bearing housing that reinforces the mount plate and takes most of the radial load off the stepper shaft, obviously…</p><p>After some trial and error, I arrived at the attached design which is working quite nicely for me. I have been able to up the max acceleration from 3500 to 4500mm/s^2 at the same quality (mind you, this is using Klipper input shaping on a BTT SKR Mini E3 V1.3, YMMV). Also, the absolute maximum accels without skipped steps increased by a similar factor, I could run slightly above 8K, though there was too much ringing for my taste even with input shaping. Still, this is as far as it will go on 12V without significantly decreasing the inertia of the X-carriage, Y could go a bit higher.</p><p>I can run significantly higher belt tension without noticeable extra load/temp on the stepper - it's easy to test and adjust if you print yourself a belt tensioner. I use <a href="https://www.thingiverse.com/thing:2854971">https://www.thingiverse.com/thing:2854971</a> for the X and <a href="https://www.thingiverse.com/thing:2869114">https://www.thingiverse.com/thing:2869114</a> for the Y axis as well as <a href="https://www.thingiverse.com/thing:2824939">https://www.thingiverse.com/thing:2824939</a> to stiffen the y motor bracket.</p><h4>You will need:</h4><ul><li>8 M3x30mm bolts</li><li>2 M3x16mm or M3x12mm bolts for the X axis endstop switch PCB - use the bolts to tap the holes in the housing, they're 2.5mm diameter and will hold it securely</li><li>2 625ZZ ball bearings (5x16x5mm)</li></ul><p>Optional: some thin (0.2-0.3mm!) washers to make sure the bearing races do not bind on the pulley. This should not be necessary, the bearings fit very snugly for me and will not move in their seat. As designed, there is 0,5-1mm play between pulley and bearing. There is also a relief bore so the inner race cannot bind on the housing and so you can remove the bearing easily.</p><h3>Print instructions</h3><p>Use PETG or something else that is stiff and does not warp easily with temperature. Steppers get warm! Also, make sure your parts don't warp while you print them or they will not work correctly and cause more binding instead of less. </p><p>I used PETG with 10% infill, 2 or 3 perimeters. Could use more, but the infill really does not contribute to stiffness a whole lot, perimeters do more. Use at least 3 bottom/top layers, 3/4 or 4/4 recommended.</p><p>The gcode files were sliced using PrusaSlicer 2.5 with a very non-stock profile. YMMV.</p><p>Only use supports for the 4 M3 bolt head holes in each bearing block - the rest does not need any if you print them so the U-shaped open side is at the top. You can easily remove these supports by poking a 2mm hex driver through the hole from the other side, they pop right out that way. The STLs are aligned the way they should be printed. Alternatively, you can use the 3MF file that is included, has all my settings and paint-on supports.</p><p>On my CR-10, the housings printed in 57 minutes (Y) and 1h3m (X) at 0.2mm layer height. Print profile is in the attached 3MF file and Gcodes, which are for a CR-10 upgraded with a BTT SKR Mini E3 V1.3 with MicroSwiss DD extruder and dual Z stepper using Klipper. </p><h3>Build instructions</h3><p>Switch off and unplug your printer just to be sure.</p><h4>X-Axis</h4><ol><li>Loosen your belt so it has almost zero tension</li><li>Disassemble the stock X stepper mount by unplugging the endstop sensor, removing the 4 short M3 bolts that hold the bracket for the X endstop switch and the two nuts and bolts holding the switch</li><li>Remove the brass hex standoffs holding the stepper</li><li>Insert one of the 625ZZ bearings into the housing, making sure you slide it all the way home and that it seats securely - you may have to glue it in place if your tolerances aren't good - calibrate your printer!</li><li>Slide the housing/bearing onto the printer shaft - should fit really snugly but go on without force, make sure it seats flush with the mount plate, push on both stepper and housing</li><li>Get the 4 M3x30mm bolts started - should all assemble without any real force, if it doesn't, check your alignment and whether your prints are straight</li><li>Tighten them diagonally in stages, so it can't bind anywhere</li><li>Give your stepper alignment a final check (should be parallel with the gantry and the housing and all flush with the mount), check you snugged all bolts equally</li><li>Use either the M3x12 or M3x16 holder clip, insert the fitting bolts through it and the endstop PCB (PCB side to the housing), align it with the bolt holes in the housing and tighten the bolts while pressing down on the hex driver - they will self-tap and hold the sensor securely in place - make sure to trim the 5 pins that stick out of the bottom of the PCB so they are <2mm long</li><li>Connect the endstop switch</li><li>Tighten the belt, making sure the carriage moves easily - you will feel if you tighten it too much</li><li>Optional: insert zip ties through the eyelets if you route your hotend cables like I do to fix them in place</li><li>Check that nothing binds and that the carriage correctly triggers the endstop</li><li>Switch it on, home it and go printing!</li></ol><h4>Y-Axis</h4><ul><li>Follow 1, 3 through 8, 11, 13, 14 above</li><li>Optional: print and mount the Y motor stiffener bracket linked above, includes instructions</li></ul><h4>Notes</h4><p>Though the housings work fine as they are now, this is still a WIP, meaning I will update this model with new versions, i.e. an integrated Y axis housing & brace that replaces the optional motor support and has a window to check belt alignment on the pulley. Also, I may add an X axis block that has a drag chain terminal.</p>
With this file you will be able to print Creality CR-10 X and Y axis stepper shaft reinforcing counter bearing housings (probably fit Ender-3 too) with your 3D printer. Click on the button and save the file on your computer to work, edit or customize your design. You can also find more 3D designs for printers on Creality CR-10 X and Y axis stepper shaft reinforcing counter bearing housings (probably fit Ender-3 too).