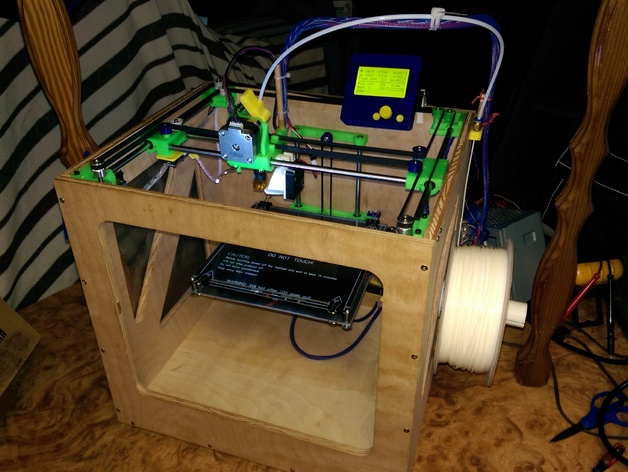
COREXY XL Printer (X3D XL COREXY by Unix)
thingiverse
Human: Remix of http://www.thingiverse.com/thing:730199 Made significant improvements and additions to the original design. Modified box DWG to utilize 12mm (11/32") plywood, eliminating LCD window and bolt slots. Box dimensions are now 408mm W x 351mm D x 386 H, Print area measures 200mm x 200mm x 213mm Z. Center carriage - drilled a 4mm hole to accommodate PFTE tube from hob-bolt into J-head, securing flexible filament in place and preventing bending. Enhanced motor mount for added stability. Left and Right carriages modified to allow deeper insertion of 8mm rods, however, this requires longer rods (328mm long on XL box). Removed the separating rib between bearings and applied a dab of RTV silicone for smooth operation. Extruder arm - added a cup to hold PFTE tube in place and resized width for optimal bearing alignment over filament. Bracket redesigned to hold LCD frame on edge of 12mm plywood. Moved Arduino/RAMPS and power supply to back of box, enhancing ease of debris removal and aesthetics. Personal preference dictates flexibility in electronics placement. Redesigned filament spool holder with a diameter of 31mm. Provided open pulley.scad file for customization using OpenSCAD for precise fit over bearing. To Do: Design a different LCD frame bracket to elevate it off the top edge of 12mm plywood or install longer ribbon cable to bring it to the front edge. Create an adjustable Z end switch flag Enclose Arduino/RAMPS with fan mount. Develop an adjustable spring tensioner on filament feed. Purchased electronics from http://www.sainsmart.com/3d-printing/3d-printkits.html Print Settings: Printer: DIY CoreXY Resolution: 0.25 to 0.35 Notes: Print 3+ perimeter, ABS hotend mounts recommended. Design Software Used: DesignSpark Mechanical for .rsdoc files QCAD 123d Design Notes: Advice: Print all idle pulleys instead of GT2 belt, as it does not ride smoothly on printed teeth pulleys. Side cutouts are optional; consider making plexiglass windows to retain heat in the box for ABS printing. Pros and Cons: Easier for first-time builders Belt on Z table lowers cost but can slip or jump due to newbie errors; still better than breaking glass. Wood absorbs vibrations, quieter than aluminum or plastic. Cons: Belt on Z can slip or stretch, only suitable for downward motion, inconsistent upward motion. 8mm rods are imperfect, causing inconsistent nozzle gap from print surface. Linear bearings do not ride smoothly, consider bushings as an alternative. Possible Improvements: Leadscrew on Z table - slow, strong, and consistent (be cautious of glass tables) Lighter/smaller extrusion stepper motor V-Slot rails instead of 8mm rods and linear bearings, which had binding issues and excessive play.
With this file you will be able to print COREXY XL Printer (X3D XL COREXY by Unix) with your 3D printer. Click on the button and save the file on your computer to work, edit or customize your design. You can also find more 3D designs for printers on COREXY XL Printer (X3D XL COREXY by Unix).