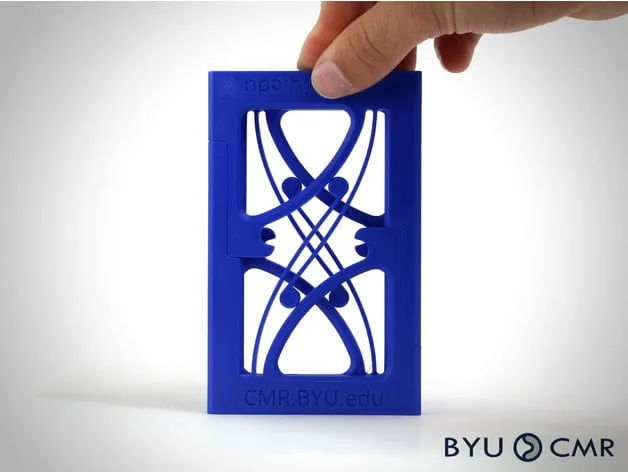
Constant-Force Mechanism
prusaprinters
SummaryThis mechanism is designed to represent a constant force mechanism, which provides a constant force through a specific range of motion. This design uses crank-slider compliant mechanism configuration with nested cams. The mechanism has a cantilever spring which deflects and travels along a cam (rigid component). As the cantilever spring deflects, a resistance force is produced. The predetermined path of the rigid component is a function of the displacement, deflection, and resistance to provide the constant force. The mechanism compensates for the varying resistance from the springs by varying the mechanical advantage, where mechanical advantage is defined as a ratio of the mechanism’s output force to input force (see more details below).The version available for download has been simplified to allow for ease of 3D printing and assembly and is meant to portray the overall concept, while not being an optimized constant-force mechanism. This 3D printable version is a single part that can be printed four times and easily snap together without the need for any additional materials such as bolts, bearings, etc.. AssemblyYou may need to actuate the mechanism multiple times before the motion is smooth and reduces friction from 3D printing flaws.Step 1: Print the part four timesStep 2: Snap parts together into two setsStep 3: Combine and align slidersStep 4: Pinch compliant beams and join parts ApplicationApplications include electrical connectors, exercise equipment, microscopic devices, and robotic end-effectors.Constant-Force Exercise MachineThis Constant-Force Exercise Machine simulates the constant force of “free weights” in fitness equipment, but using compliant members in a crank-slider configuration instead. This machine replicates the benefit and “feel” of free weights without the hassle and danger of heavy weights. Other exercise equipment utilize weight stacks or springs to create resistance, however weights stacks are heavy and bulky and traditional spring mechanisms don't provide constant resistance (i.e. resistance increases with displacement).This machine creates a constant force over a given distance or deflection.Advantages of a constant-force exercise machine include: 1) 'Feels' like free weights, 2) cost less, 3) weigh less, 4) more compact, 5) safe, 6) simple. Constant-Force End-EffectorThe design consists of four constant-force compression springs, a cage, and two piston assemblies. The key components of the design are the constant-force springs. This particular configuration consists of a long flexible segment pinned to a rigid segment, with the opposite ends of the flexible and rigid segments fixed and pinned, respectively.When mounted as a coupling device between a robot manipulator and its end-effector, a constant force can be applied to a surface. For example, a robot using this mechanism can score a pane of glass without breaking it, even with significant misalignment between the robot tool path and the pane of glass. Constant-Force Electrical ContactStudies show that 85% of all automotive electrical problems are a result of contact integrity problems while over 70% of all computer hardware problems can also be traced back to contact problems. The constant force electrical contact consists of a polypropylene slider and two small spring steel inserts. The combination of flexible segments and slider geometry combine to allow the slider to output a constant force thus promising to improve the performance of electrical contacts. Learn MoreCompliant MechanismsA mechanism is a mechanical device that transfers or transforms motion, force, or energy. Compliant mechanisms are unique in that they function through the deflection of their flexible members. This is unlike traditional rigid-body mechanisms that achieve their motion through discrete parts that are connected by moving joints.Advantages of compliant mechanisms include cost reduction and performance advantages over rigid-body mechanisms. Because they achieve their motion through the deflection of flexible members, they have fewer parts, reduced wear, reduced part counts, and higher precision.These advantages are helpful in the development of a constant-force exercise machine, because compliant mechanisms can achieve the desired performance with fewer parts and lower weight than other alternatives. Constant-Force MechanismsThe fundamental principle of constant force mechanisms is that it compensates for varying resistance of the deflected spring by using varying mechanical advantage. By applying compliant mechanisms in a crank-slider configuration, the mechanical advantage of the system changes with displacement, creating a constant resistance.Unlike regular linear springs which yield an increased force with greater displacements, constant- force "springs" combine the effects of mechanical advantage and stored strain energy of flexible members to obtain a constant output force over a large range of displacements.This design was developed by the Compliant Mechanisms Research Group (CMR) from Brigham Young University (BYU). Follow us at @byucmr on Instagram or visit the BYU Compliant Mechanisms Research (CMR) website to learn more about compliant mechanisms.Also available is a free online course on compliant mechanism design, by Dr. Jonathan B. Hopkins, Ph.D., UNLC.https://www.youtube.com/watch?v=S4o6-wXmwaQ&list=PLWeErkRyxkhJv-ynwCvM0XxKusTJJQzJl Technical InformationFor in-depth technical information, see the following publications: Tolman, K.A., Merriam, E.G., and Howell, L.L., “Compliant Constant-Force Linear-Motion Mechanism,” Mechanism and Machine Theory, Vol. 106, pp. 68–79., DOI: 10.1016/j.mechmachtheory.2016.08.009, 2016, Boyle, C., Howell, L.L., Magleby, S.P., and Evans, M.S., “Dynamic Modeling of Compliant Constant-Force Compression Mechanisms,” Mechanism and Machine Theory, Vol. 38, No. 12, pp. 1469-1487, 2003. Weight, Brent, “Development and Design of Constant-Force Mechanisms,” M.S. Thesis, Brigham Young University, December 2001. To learn more about compliant mechanisms in general, see the BYU Compliant Mechanisms Research (CMR) website or these books: Compliant Mechanisms, Handbook of Compliant Mechanisms Intellectual PropertyThe downloadable 3D print files provided here may be used, modified, and enjoyed for noncommercial use. To license this technology for commercial applications, contact:BYU Technology Transfer Office3760 Harold B. Lee LibraryBrigham Young UniversityProvo, UT 84602Phone: (801) 422-6266 https://techtransfer.byu.edu/contact Patent Information“Substantially Constant-Force Exercise Machine,” Howell, L.L. and Magleby, S.P., U.S. Patent No. 7,060,012, issued June 13, 2006.“Constant Force Apparatus and Method,” Weight, B.L., Mattson, C.A., Magleby, S.P., Howell, L.L., and Brown, B.J., U.S. Patent No. 6,945,800, issued September 20, 2005.“Compliant Constant-Force Mechanism and Devices Formed Therewith,” Midha, A., Murphy, M.D., and Howell, L.L., U.S. Patent No. 5,649,454, issued July 22, 1997.For licensing questions, please reach out to Spencer Rogers (srogers@byu.edu, (801) 422-3676)
With this file you will be able to print Constant-Force Mechanism with your 3D printer. Click on the button and save the file on your computer to work, edit or customize your design. You can also find more 3D designs for printers on Constant-Force Mechanism.