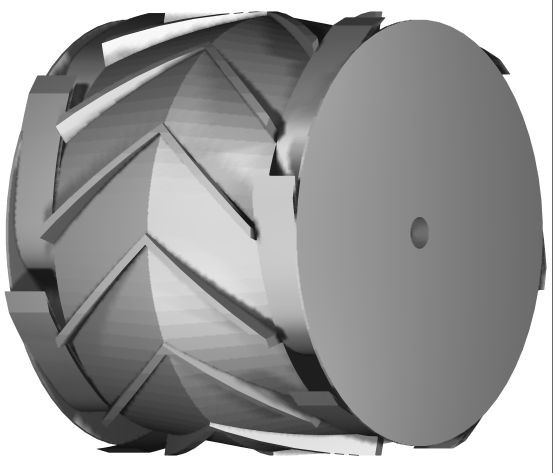
Chevron Drum
grabcad
My Drum design encompasses the entire allowable dimensions, measuring 450 mm in diameter and 360 mm in width. A 1:4 scale model, tested with builders sand, has consistently achieved a fill rate of 58%, while a full-scale drum could potentially reach >60%. The chevron 'tread' and slight taper of the drum direct loose material to the edges, where (6) scoops at each end ingest an amount of material, filling their cavities. As the drum rotates, the scoop cavity contents are lifted, causing the additional weight to open an inner flap, allowing the material to fall into the drum interior from a high position. Drum contents lower down keep other flaps closed and sealed, preventing them from falling out. As the drum fills, it reaches a point where the flaps are prevented from opening; this point is determined by the rill angle of the material or its tendency to clump together. This point can be extended by vibrating the drum or using a pulsed drive. To empty the contents, the home-base processing facility requires an 'unloading station' that the device drives into, containing a mechanism to push against the end of the drums. When pressed and released, the drum splits apart at the middle, allowing the contents to quickly spill out (assisted by the taper). When empty, pressing again brings the two drum halves back together and locks them closed. The mobile device's primary function is to travel to site, load material, and return to home-base; the unloading station should handle this process. It would be preferable to incorporate a method for unloading into the stationary home-base facility rather than add complexity or weight to the mobile device. The drum will be constructed of Titanium using 3D printing, combining the scoop end and inner drum half as one piece, with the other half being a mirror image. The flaps will be made of a flexible elastomer (such as silicone) with variable thickness (stiffness), located over the inner end of each scoop cavity. With a Titanium density of 4.6 gr/cm³, the overall weight would be approximately 4.78 kg. To reduce wear, it could be coated with diamond via chemical vapor deposition (CVD), which would put it above the 5.0 kg limit. If reducing wear is a high priority, the drum width could be reduced to suit and possibly still provide the minimum 17.5 Lt capacity. The STL provided of the drum was simply scaled up from that used for the plastic model, so does not represent the actual wall thicknesses (mostly 0.8-1.0 mm) if printed at full-size in Titanium. Nor does it show the flap configuration or open/close mechanism. Although not part of the competition, I have several other ideas related to the overall RASSOR device, including seals, wheels, and overall length.
With this file you will be able to print Chevron Drum with your 3D printer. Click on the button and save the file on your computer to work, edit or customize your design. You can also find more 3D designs for printers on Chevron Drum.