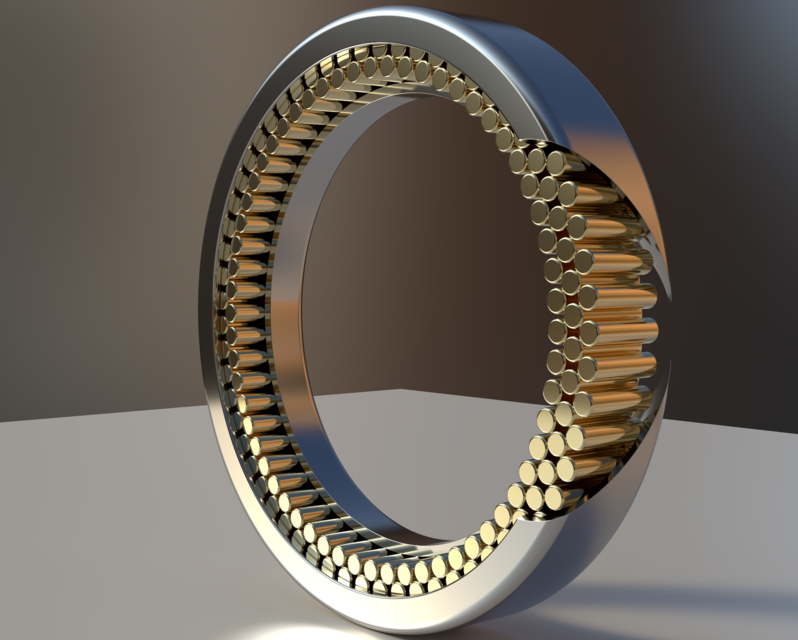
Cageless, Multilayered, Full Complement Radial Roller Bearing
grabcad
First among several innovative rolling element bearing concepts I conceived between late 2013 and early 2014 was a principal design that featured no sliding contact between consecutive rollers within the same row or layer of rolling elements. Unlike traditional bearings, this one didn't rely on a single cage to keep the rollers apart; instead, it used multiple layers of rollers that intermeshed with each other. Specifically, three distinct layers were employed: an inner and outer layer, as well as an intermediary separating layer that acted like a load-bearing rolling cage. This middle layer effectively kept consecutive rolling elements in the other two layers from touching each other, ensuring smooth rotation without excessive friction or resistance. The use of an odd number of layers was crucial to prevent the rollers from attempting to convey rotation between the bearing's inner and outer races. If even-numbered rows were used, they would actually work against the bearing's purpose by enabling rotation in the opposite direction. Using just two layers would have required the rolling elements to travel at impractically high speeds, rendering the design impractical. With only one row of rollers, the bearing would be no different from those commonly used today, featuring sliding contact between consecutive rolling elements or between these and a non-load-bearing cage that kept them separated. The innovative bearing design features a middle layer of rollers that separates and prevents sliding contact between any two consecutive rollers in either the first and third/last layer. This middle layer acts like a rolling cage analogous to the sliding cage found in traditional roller bearings, which typically have only one row of rollers. Conversely, consecutive rolling elements in the middle layer are kept apart by rollers in the inner (first) and outer (third) layers. The primary purpose of this 'rolling cage' middle layer is not just to keep consecutive rolling elements separate; it also conveys the load from the bearing's inner layer to its outer one. This design inherently accommodates rolling elements with slightly different radii due to manufacturing tolerances, balances loads evenly across the rolling elements despite possible unevenness in roller diameter, and appears to be self-centring. In an effort to bring this concept to life, I submitted detailed documentation outlining the design to various corporations operating in mechanical engineering, machine, vehicle, or device manufacturing. Companies like Bosch and the Schaeffler Group were approached, but unfortunately, my submission garnered no attention or interest from any of these companies. Perhaps the design is fundamentally flawed or impractical, rendering it worthless, and I simply didn't realize this myself due to a lack of formal education in mechanical engineering or other fields.
With this file you will be able to print Cageless, Multilayered, Full Complement Radial Roller Bearing with your 3D printer. Click on the button and save the file on your computer to work, edit or customize your design. You can also find more 3D designs for printers on Cageless, Multilayered, Full Complement Radial Roller Bearing.