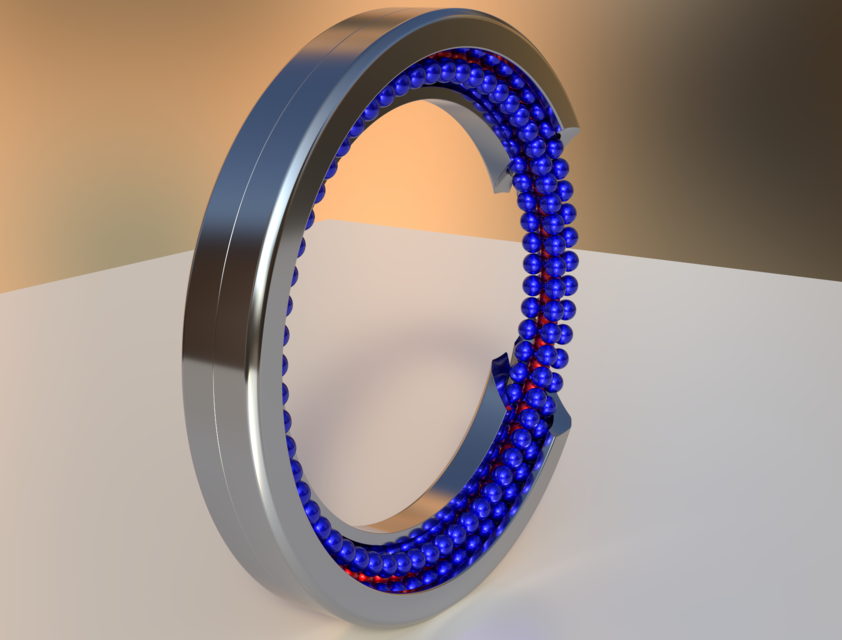
Cageless, Multilayered, Full Complement Radial Ball Bearing
grabcad
Second of several different rolling element bearing concepts I came up with back in late 2013 – early 2014. Unlike the first bearing design, this one supports significant axial loads as well, in addition to mainly radial loads, without a significant increase in friction or frictional losses. This required spherical rolling elements instead of cylindrical ones, as used in the first concept. The innovative aspect is that even though the bearing is full complement and cageless, there's no sliding contact between consecutive rolling elements inside it. Nor are balls kept apart by a single common cage they'd all rub against rather than each other. This is due to 3 inter-meshed layers of spheres: an inner layer, an outer layer, and an intermediary separating layer which acts as a load-bearing rolling cage and keeps consecutive rolling elements in the other two layers from touching each other. An odd number of layers of balls are necessary because using an even number would attempt to convey rotation from the bearing's inner race to its outer one, working against the purpose of the bearing. Using just two layers would mean spinning the bearing requires balls to travel at a proportionally impractically high rate of speed. Because of this, the bearing has to have an odd number of layers of balls. And using just one row of rolling elements would be no different than regular bearings in use today, which exhibit sliding contact either between consecutive rolling elements or between these and a non-load-bearing cage that keeps them separated. The middle layer of spheres separates and prevents sliding contact between any two consecutive balls in either the 1st and 3rd/last layer, acting as a sort of rolling cage analogous to the sliding cage in a regular ball bearing. Reciprocally, consecutive rolling elements in the middle layer are kept apart by balls in the inner (1st) and outer (3rd) layers. The purpose of the 'rolling cage' middle layer isn't just to keep consecutive rolling elements separate, it's also load-bearing as it conveys the load from its inner layer to its outer one. Other envisaged benefits include automatic accommodation of slightly different radii occurring due to manufacturing tolerances and even distribution of load across rolling elements despite possible unevenness in ball diameter due to manufacturing tolerances. It should also be self-centring. I attempted to submit this idea to various corporations operating in mechanical engineering, machine, vehicle or device manufacturing, but unfortunately it didn't seem to garner any attention or interest from the companies I approached. The design has never been patented by myself and I wasn't demanding compensation for it, only asked to possibly be considered for hiring or reimbursed collaboration. Unfortunately, that did not come to pass. Perhaps the design is fundamentally flawed or impractical and therefore worthless, but I just didn't realize this myself, lacking training or formal education in mechanical engineering.
With this file you will be able to print Cageless, Multilayered, Full Complement Radial Ball Bearing with your 3D printer. Click on the button and save the file on your computer to work, edit or customize your design. You can also find more 3D designs for printers on Cageless, Multilayered, Full Complement Radial Ball Bearing.