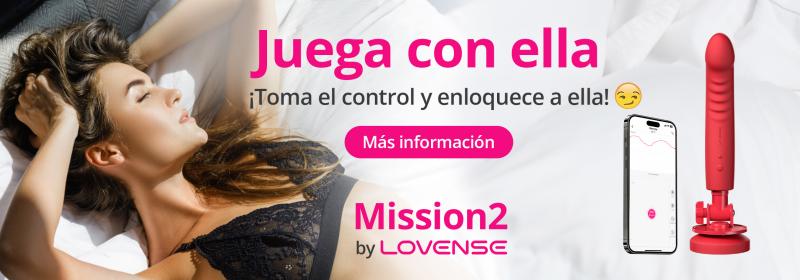
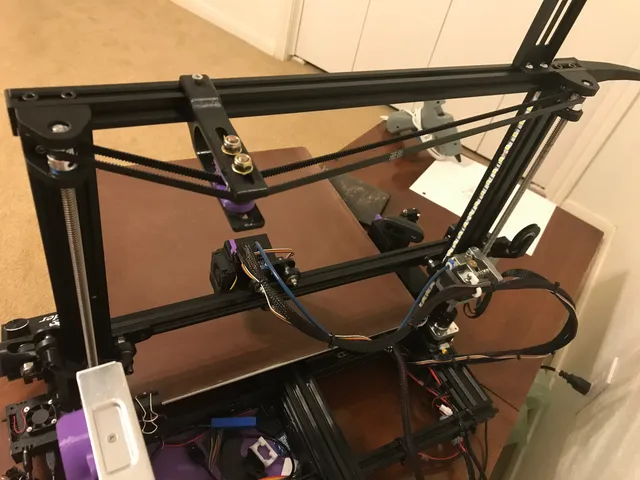
Biggus Dickus Dual-Z Conversion - Ender 3
prusaprinters
Partially original, partially remixed (attributions later in this section). Provides a solid dual-Z conversion using parts you may already have laying around, or are at least cheap and easy to get. This was for my Ender Extender converted (400mm x 400mm) Ender 3 but should work with many others including a stock Ender 3.Looking for a power supply relocation solution? You will need one - I have that here.Items to ProcureYou will need:An appropriately sized 2nd lead screw. For my printer with 250mm Z height, I chose a 400mm T8x8. It's important to make sure it matches your original lead screw (for example for most Creality printers and clones, 8mm diameter, 2mm pitch, 4 starts, equals 8mm lead). I believe that a screw as short as 320mm would have also worked.Another lead screw nut - like the one which is brass on the original lead screw.You can use the same type as the original nut (Option 1), or the more universal RepRap style that comes included with many threaded rods (Option 2). I highly recommend upgrading to POM material, as this helps reduce binding and doesn't need constant lubrication. Link here. GT2 timing belt, closed loop. I cannot comment on which size is needed for stock Ender 3 using my tensioner design, but for my 400mm X/Y conversion, a 1000mm belt is the right size. Do not get a belt which requires you to splice the ends together yourself unless you know exactly what you are doing.8x quantity of 688-2RS ball bearings, such as these.2x quantity of GT2 pulleys, 20 teeth, with 8mm bore. Such as these.(Optional) for lower Z bearing brace: a single 608-ZZ type ball bearing.Tensioner hardware:2x quantity of M6 x 35mm bolts (you can use longer bolts with no problems)4x quantity of M6 flat washers2x quantity of M6 lock nuts1x quantity of M4 screw with T-nut for mounting (forget exact length)Z Bracket hardware:1x quantity of M5 x 25mm bolt. 30mm to 40mm can be made to work.2x quantity of M5 x 35mm bolt. 40mm and 45mm can be made to work.3x quantity of M5 lock nutsHardware for the lead screw nut, will vary. Typically, short M3 or M4 screws.Hardware for upper pulley carriers:8x M4 screws with T-nuts… I forget the length, I think 12mm?Make sure the GT2 pulleys include the grub screws.Hardware for lower Z brace:2x M4 screws with T-nuts… I again forget the length, 12mm?----------------------------------------------------Belt Tensioner AssemblyAttribution: This is an original part.Printing Notes:Recommend PETG strongly! PLA may buckle over time.Print the tensioner on its side.Print 2x of the bearing brackets, with the sleeves facing up.Tree supports may be used as required.Use ~50% infill.Use 0.5mm line width preferably, with 3 or 4 perimeters.Installation:The 688-2RS bearings will snap into place on the bearing brackets, you will use 4 in total.Route the belt as shown in the attached images, sandwiching the bearing brackets around the belt. Then, you can slide the brackets into the main tensioner part.Install the M6 bolts through the slots in the tensioner, lined up with the holes through the bearings. Ensure a washer is used on each end up the bolts so it spreads the load over more area. Follow with the locknuts, leaving them loose at first. Z Bracket AssemblyAttribution: This is remixed from the Proper Printing part, here.About the two options:Option 1 has been modified to accept the Ender-3 style lead screw nut. It will sit on top of the bracket, with the mounting flange on the upper face of receptacle. See images.Option 2 uses a generic RepRap lead screw nut, which has 4 holes and is round. Both options have been modified so the V-slot rollers will not contact the bracket (a small lip is there, which contacts the bearing inner race and spaces it away).About the spacers:The 0.36mm spacer is there if the V-slot rollers are still dragging on the bracket when they spin. Put these between the rollers and the bracket to space them out.The 5mm and 10mm spacers are for using longer hardware… I had a few M5 bolts but none were the perfect length so I used these. You can scale them in your slicer to be any length.Printing Notes:Recommend using a durable material like PETG, Nylon, ASA, etc.Print the bracket with the 3 arms facing the bed.Supports should be used, especially where the 3 arms meet the bed, as there is a lip. Tree supports did not generate at these locations in my case so I used the normal support type.Use ~50% infill.Use 0.5mm line width preferably, with 3 or 4 perimeters.Installation:Installs just like other brackets which you can get online - see those instructions or Youtube videos.For all 3 of the M5 bolts, make sure the socket head is facing the back of the printer. You will otherwise struggle with holding the hex nut during tightening, as they will be recessed in the bracket.Install the lead screw nut.Note that the holes are slightly oval, to allow adjustment and alignment before tightening. Upper Carrier AssembliesAttribution: This is from fdumi on Thingiverse, here.Printing Notes:Recommend using a durable material like PETG, Nylon, ASA, etc.Print 2 brackets and 4 of the spacers.Tree supports recommended.Use ~50% infill.Use 3 or 4 perimeters.Installation:Start by pressing the 688-2RS bearings into each of the carriers, each one takes 2.A spacer goes on each side of the GT2 pulley, which will then contact the bearings.Orientation of the pulley should match the pictures, that is, the grub screws on the lower half.You will need to be steady, as you line up a lot of components… the lead screw, bearings, spacers, and the pulley which has the belt already wrapped around it.Mount the carriers using the M4 hardware and T-nuts. The upper hardware goes into the 2020 gantry (side to side) and the lower hardware goes into the 2040 vertical extrusion.Note that the holes are slightly oval, to allow adjustment and alignment before tightening. Lower Z Brace AssemblyThis piece is 100% optional. It goes at the base of the 2nd lead screw. I ended up not using it, as my cheap lead screw wasn't perfectly straight and this would have caused binding.Attribution: This is remixed from Don's bracket, here.About the versions:20mm spacing is my remix, which fits the 2040 extrusion of the Z axis.15mm spacing is the original version. For mounting on horizontally oriented extrusions.Printing Notes:Recommend using a durable material like PETG, Nylon, ASA, etc.Tree supports recommended.Use ~50% infill.Use 3 or 4 perimeters.Installation:Press in 608 size bearing.Loosen the grub screws on the pulley so you can slide the lead screw up and down.Install to extrusion using M4 hardware and T-nuts. Set height and tighten.Line up the lead screw and check alignment. There are M4 shims included to push the brace out if needed.Before stabbing the lead screw through the bearing, spin it, to check for straightness. If you have visible run-out, I would strongly suggest not using this brace.
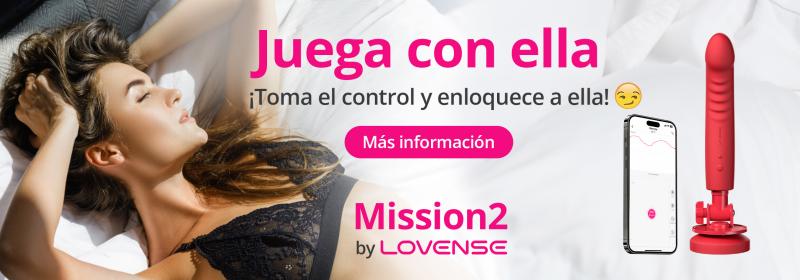
With this file you will be able to print Biggus Dickus Dual-Z Conversion - Ender 3 with your 3D printer. Click on the button and save the file on your computer to work, edit or customize your design. You can also find more 3D designs for printers on Biggus Dickus Dual-Z Conversion - Ender 3.