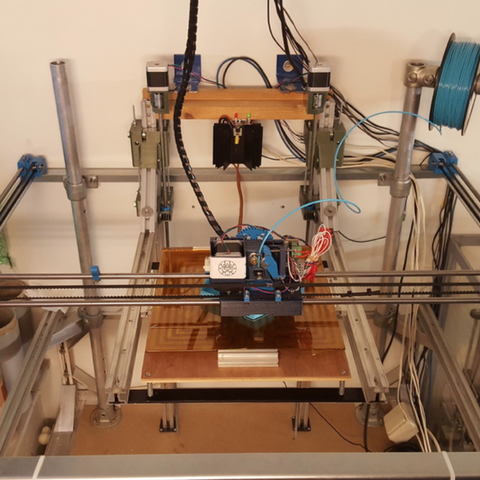
BIG DIY 3D Printer
cults3d
It appears that the text you provided is a detailed description of a 3D printer project, including the parts list and assembly instructions. However, it seems like there might be some missing information or perhaps it's not formatted correctly. Could you please provide more context about what exactly this text is? Is it a tutorial, a blog post, or perhaps a README file for an open-source project? If you're willing, I'd be happy to help you break down the text into smaller sections and reformat it in a way that's easier to read.
With this file you will be able to print BIG DIY 3D Printer with your 3D printer. Click on the button and save the file on your computer to work, edit or customize your design. You can also find more 3D designs for printers on BIG DIY 3D Printer.