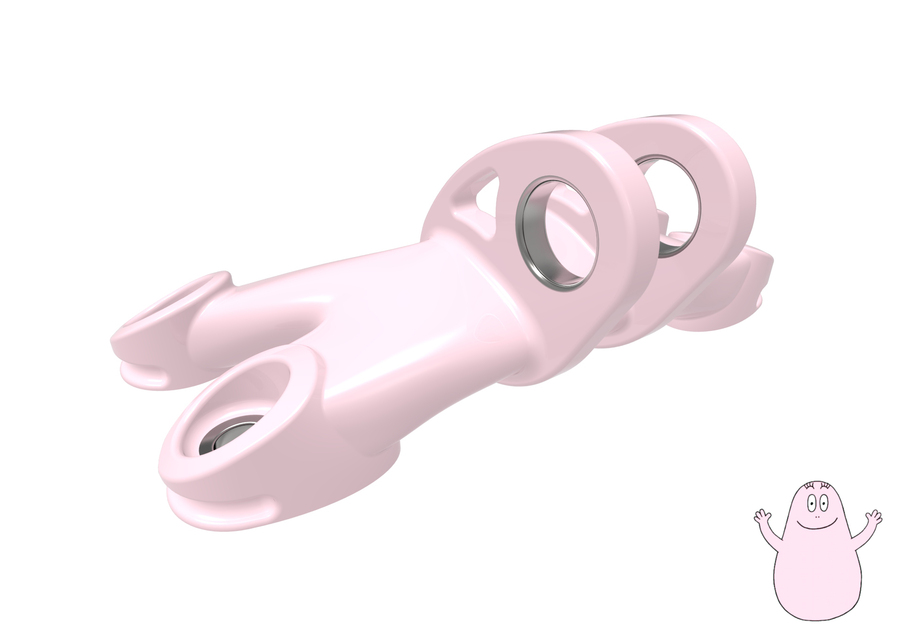
BarbaBracket
grabcad
The initial goal was to showcase the potential of additive manufacturing through an uncomplicated yet innovative design. By replacing the original solid block with an organic curved shape, optimized based on FEA stress directions and magnitudes, a weight reduction of 78.3% was achieved, with all maximum stresses remaining below 131 ksi. The model was created using CREO 2.0's surface modeling tools in combination with freestyle, allowing for the creation of unique shapes reminiscent of Barbapapa. The simulation process was time-consuming but crucial to ensure a reliable result. A floor-contact surface was incorporated into the assembly to simulate realistic conditions. The P-type multi-pass adaptive analysis in CREO 2.0 Simulate provided accurate results without requiring conversion to STEP format. Local horizontal bolt areas were excluded from stress calculations to avoid inaccurate peak stresses. Adding a hole in a low-stress area further contributed to weight reduction, while also being essential for additive manufacturing processes. Detailed information on the FEA analysis can be found in the provided PDF files.
With this file you will be able to print BarbaBracket with your 3D printer. Click on the button and save the file on your computer to work, edit or customize your design. You can also find more 3D designs for printers on BarbaBracket.