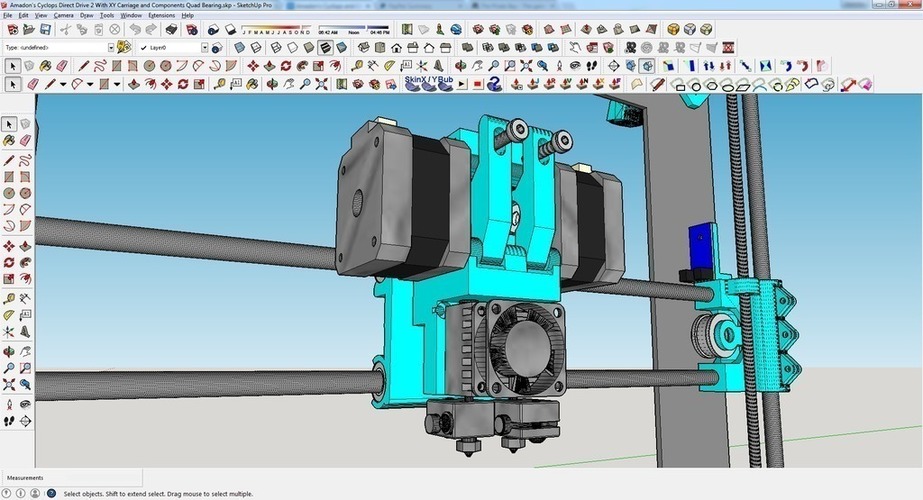
Amadon's Cyclops and Chimera Direct Drive Version 3
pinshape
SummaryEDIT: 6/28/16 A V4 of the extruder body has been added, featuring holes for PTFE tubing that go all the way through. This allows users to create their own cutouts for the drive gear without worrying about precise length requirements. EDIT 6/6/16 New idlers have been designed with support for bearings on both sides, preventing bending and loss of clamping pressure on the filament. A 0.4mm thick support material is built into each idler, eliminating the need for additional support from a slicer. Low profile nuts are recommended, along with washers on both sides of the roller bearing. The flat side of the idlers should face towards the motors, while slightly raised sides face towards the center. The nut should be placed on the motor side. A complete printer was previously included here, but its title did not make sense, so it has been published separately: http://www.thingiverse.com/thing:1259225/ This is an updated and more reliable version of my previous thing seen here: http://www.thingiverse.com/thing:961555 The primary difference between this V4 and the previous version (V2) is that PTFE tubes are no longer cut off flush with the top of the cold end. Instead, they extend into the extruder body just below where the gear feeds the filament through the hole. This reduces bind points since the extruder top does not need to line up perfectly with the bottom of the body. The PTFE tubes in my print are 47mm long, but users should initially cut them to about 50mm and try assembling the cold end. If they are too long, trim off about 1mm and repeat until the PTFE tubes are exactly the right length, snug but allowing holes on the back of the cold end to match up with the printed extruder body. TIP: Do not make the PTFE too snug, as this can cause problems. If it is too long, it will soften and try to squeeze into a U-shaped reduction in diameter at the bottom, causing binding. I had mine slightly too long, by about 1mm, which resulted in having to heat my hot end enough to liquify the PTFE and push the filament through by hand until I extruded the PTFE touching my filament. This was a big pain. To avoid this issue, make sure your PTFE is exactly the right length or put it together without heat brakes inserted all the way and then move them up. Then level them. The difference between the two X carriages is minor. The Chimera one has easier access to upper rear grub screws on the cold end and allows users to slide lower bearings out of the way to get to lower grub screws. Parts needed: * 2 MK8 drive gears * 3 M3 threaded rods (120mm long) * 2 springs (trim shorter and use trial and error for tension) * Washers for M4 screws (to keep springs from slipping past screw heads) * Ball bearings (5x10x4) * Idlers with washers between idler and ball bearing * M4 nuts for idlers Configuration.h can be downloaded here: http://pastebin.com/4izq94YL. It's configured to use a Chimera, but users with a Cyclops should change (#define EXTRUDERS) to 1. A custom printer name "augmentation" was given so it would say "augmentation ready" when ready to print. Users can change this to whatever they like. If any screws or parts were missed, let me know! Thanks and enjoy! EDIT: Access holes for mounting screws for Chimera/Cyclops have been added in the X carriage, making it easier to tighten them without disassembling anything. https://www.youtube.com/watch?v=T9Ya5-5jXGc
With this file you will be able to print Amadon's Cyclops and Chimera Direct Drive Version 3 with your 3D printer. Click on the button and save the file on your computer to work, edit or customize your design. You can also find more 3D designs for printers on Amadon's Cyclops and Chimera Direct Drive Version 3.