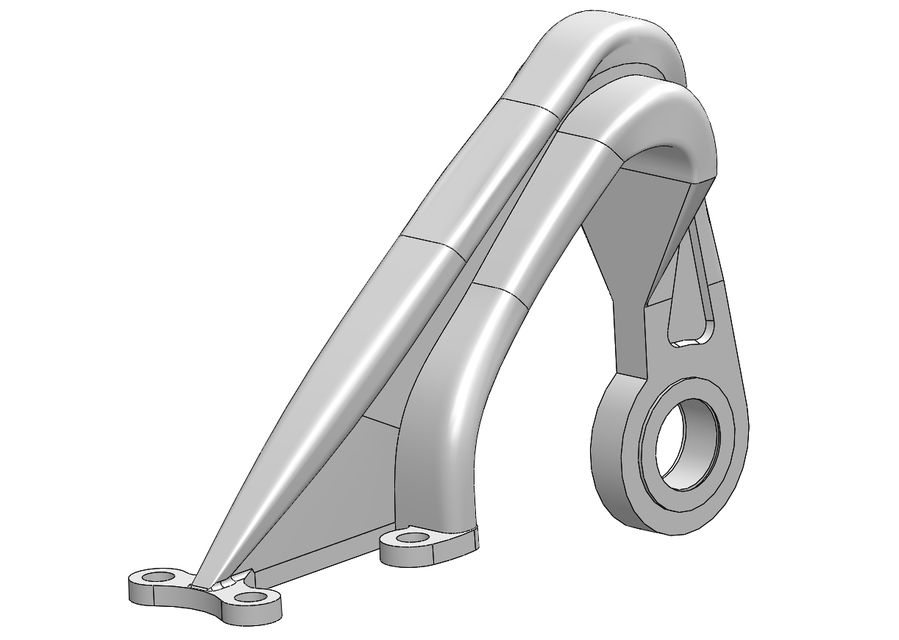
Airplane Bearing Bracket Challenge
grabcad
The Airplane Bearing Bracket Challenge aims to enhance airplane bracket design by optimizing weight, strength, and additive manufacturing processes. Additive Manufacturing (AM) offers significant advantages over traditional techniques, such as placing materials only where necessary for performance and creating complex shapes with ease. In this redesign project, the current design is analyzed to identify critical stress locations, considering factors like bearing interface, 4 bolt portholes, support interface, and work envelop. The "Von Mises equivalent stress" method is used to calculate stresses, while ensuring individual principle stresses are lower than the yield strength. Through iterative design and strength analysis, a submitted design achieves a volume/mass reduction of 69%. Further optimization is possible but not pursued due to increased calculation time. AM has limitations, including platform size constraints, layer distance, grain size, and directional strength differences. Support structures are necessary for overhanging parts and heat dissipation. Post-processing includes heat treatment, EDM or milling, and removal of support structures. Since strength is most critical, the building layers should be parallel to the plane through all load cases, with 0.045-inch support thickness adding 0.16 lbs to printed material.
With this file you will be able to print Airplane Bearing Bracket Challenge with your 3D printer. Click on the button and save the file on your computer to work, edit or customize your design. You can also find more 3D designs for printers on Airplane Bearing Bracket Challenge.