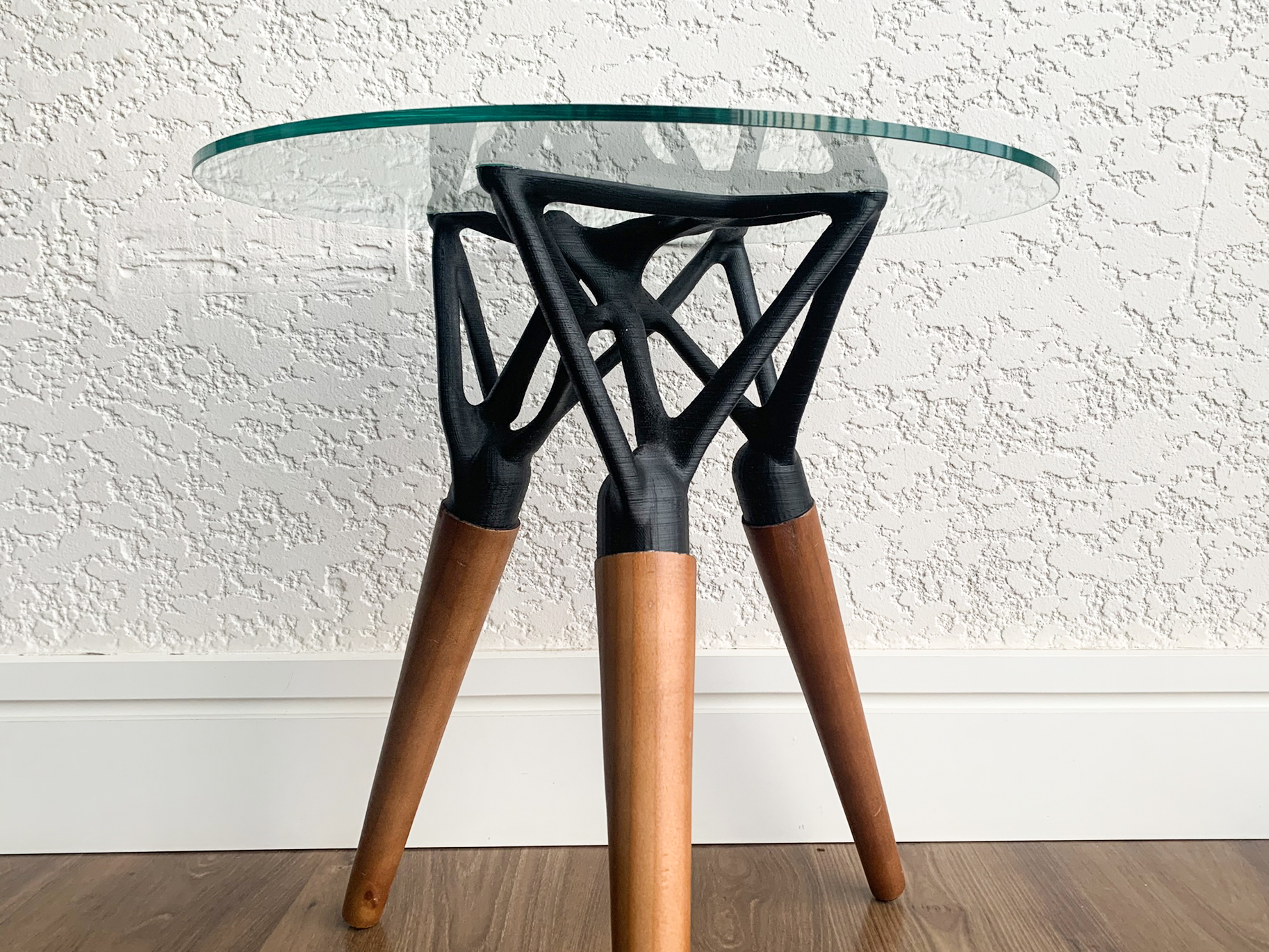
AI-designed table
prusaprinters
<h3>About the Projec<strong>t</strong></h3><p>This project was inspired by the side tables from the <a href="https://www.morganfurniture.co.uk/collection/rio/">RIO collection</a> (by Morgan Furniture), which used 3D printed parts created by algorithmic design tools. They have a distinctly organic feel, yet they are purely functional and designed to withstand day-to-day uses.</p><figure class="image image-style-align-left image_resized" style="width:36.87%;"><img src="https://media.printables.com/media/prints/201026/rich_content/2da3ed13-fb38-419f-91dd-c030afbce019/img_8889.jpeg#%7B%22uuid%22%3A%2244eea03a-0335-4563-b1da-27382fd461be%22%2C%22w%22%3A1536%2C%22h%22%3A2048%7D"></figure><p>I've been playing around with Fusion 360's generative design for a while now, and I knew it could make something similar. <a href="https://onezero.medium.com/generative-design-disruption-hype-or-threat-ab7ef52aa1f2">Generative design</a> is an AI-based computational tool that creates optimized geometries based on a few criteria, such as supported weight, material, manufacturing processes, physical constraints, among others.</p><p>We have little control over how the parts will look, but I was happy with the results after just a couple of tries. It has a unique look, and the table itself turned out to be quite sturdy (as expected).</p><p>The table has been in use for almost a year now - without any issues whatsoever - successfully enduring day-to-day use, tabletop gaming, and even a couple of lazy cats. </p><p> </p><h4>Materials</h4><p>From the start, the idea was to use tapered wooden legs and a glass table top to enhance visibility. Here's the complete list of materials:</p><ul><li>1x Tempered glass table top (4 mm thick and 450* mm in diameter)</li><li>3x Tapered wooden legs (around 350 mm in length and 45 mm large-end diameter)</li><li>3x Double-ended M8 (or 5/16) dowel screws</li><li>Transparent double-sided tape</li><li>Around 650 grams of PETG filament (more depending on the support structures required by your 3D printer)</li></ul><h4>Assembly</h4><p>The assembly is very straightforward. Once printed, the few support structures used were removed, and I just lightly sanded the surfaces on the top where support structures were used. I also gave it a light coat of black paint, not enough to cover the 3D printing lines since I kinda enjoy them, and I feel they help tell the story.</p><p>The legs were attached to the 3D printed part with double-ended M8 dowel screws threaded directly into the plastic through pre-designed holes. The table top was fixed to the 3D printed body with (good) double-sided tape. And that's it. </p><h3>The Design Process</h3><p>Let's quickly go over the design process for this specific project using this Fusion 360 feature so everyone can have at least an idea of how it works. In a nutshell, we need to set a few criteria for the part to be created so the algorithm can come up with different design solutions that fit all the requirements. </p><figure class="image image-style-align-right image_resized" style="width:36.92%;"><img src="https://media.printables.com/media/prints/201026/rich_content/958e870a-a507-4675-8b33-d2979e9bbd77/screenshot-2022-06-07-182826.jpg#%7B%22uuid%22%3A%22edc7c535-f685-4062-ab4e-b92d82db3178%22%2C%22w%22%3A638%2C%22h%22%3A696%7D"></figure><p>I started by 3D modeling the outsourced parts - furniture legs and tabletop (in red) - and positioning them as they will be once assembled. This includes setting up the total height of the table as well as the part.</p><p>Then, I modeled the components (in green) that will interface with the outsourced parts. These components will be preserved and incorporated into the final design as a way to guarantee a proper assembly later on. </p><p>Another major step in a generative design workflow is to set the physical constraints and forces/moments involved. </p><p>I made a free body diagram of each part and calculated all possible loading conditions considering the different positions objects can be placed. I also considered the loads involved in moving the table around — lifting, lateral movement, and rotation.</p><figure class="image image-style-align-left image_resized" style="width:43.4%;"><img src="https://media.printables.com/media/prints/201026/rich_content/30b4ede5-6730-420b-9e56-7e5793983b81/ezgifcom-gif-maker.gif#%7B%22uuid%22%3A%22c344a2c6-9e7b-45d6-b6ae-c91e5d0443da%22%2C%22w%22%3A351%2C%22h%22%3A364%7D"></figure><p>The table’s maximum capacity was calculated according to my cats’ weight. They always fight over the best (and oddest) spots to sleep, so I settled for their combined weight with a few kilograms to spare (around 15 kg). </p><p>Finally, a few more criteria and goals had to be set up like the part's material (PETG), safety factor (2.5), and the manufacturing process (3D printing). I also set the maximum overhang angle for my 3D printer (60°) so the software can optimize the design to reduce the amount of support structures required. </p><p>All that was left was to start the generative design process. After a few hours, a handful of design solutions that fitted all the above criteria were presented, and I picked the one that was the sturdiest and the prettiest (to my taste). </p><p>If you want to know more about the generative design process, I wrote <a href="https://onezero.medium.com/generative-design-disruption-hype-or-threat-ab7ef52aa1f2">an article</a> about it that goes over its main aspects.</p><h4>3D Printing</h4><figure class="image image-style-align-right image_resized" style="width:37.14%;"><img src="https://media.printables.com/media/prints/201026/rich_content/1a2095fd-cb0c-4193-801b-623e819d91c5/screenshot-2022-06-07-183151.jpg#%7B%22uuid%22%3A%2286ddfe00-a643-46ef-b6bb-f83a84f431dd%22%2C%22w%22%3A800%2C%22h%22%3A771%7D"></figure><p>The final part was sliced and printed in PETG with the following settings:</p><ul><li>Layer height: 0.20 mm</li><li>Solid layers: 8 (top & bottom)</li><li>Contours/perimeters: 4</li><li>Infill: 55% (rectilinear) </li></ul><p>Although optimized, support structures were still required. I manually added the support structures since I know how well my 3D printer handles overhangs, but I strongly suggest you follow your own workflow.</p><p>The printing itself took around <strong>35 hours</strong> in total to print and, fortunately, I got it right on the first try.</p><h3>I hope you like it and maybe try it yourself! Here's Leia enjoying it: </h3><figure class="image image_resized" style="width:82.79%;"><img src="https://media.printables.com/media/prints/201026/rich_content/906b8e99-b02f-44ba-8d3b-66fc5bb11188/img_8993.jpeg#%7B%22uuid%22%3A%2238f78a9f-60da-4eca-90b4-981ecbce4d4f%22%2C%22w%22%3A2048%2C%22h%22%3A1536%7D"></figure><figure class="image"><img></figure>
With this file you will be able to print AI-designed table with your 3D printer. Click on the button and save the file on your computer to work, edit or customize your design. You can also find more 3D designs for printers on AI-designed table.