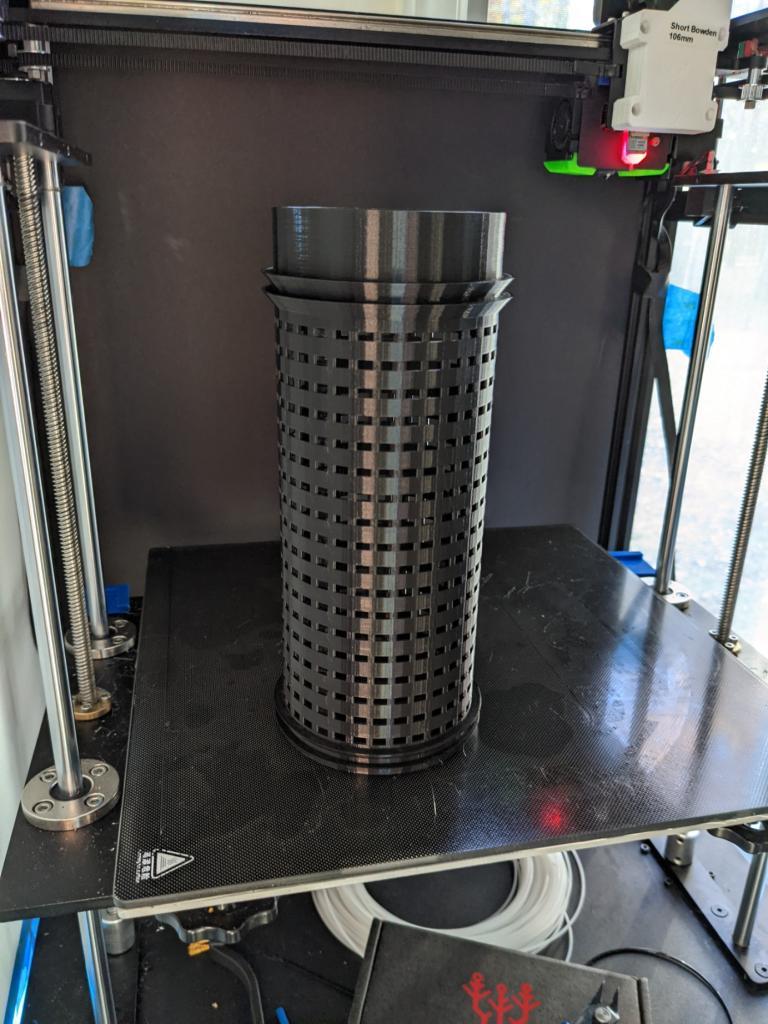
Activated Charcoal Negative Pressure Air Filter
prusaprinters
<p>I wanted an activated charcoal air filter for the flip top LACK enclosure of my Qidi 6.08 mono resin printer. There was sufficient room in the enclosure for a fairly large filter element. I built a filter core sized around the intake of a radial blower. The core was then wrapped with a thick activated charcoal pad. Flanges on either side of the foam board enclosure wall hold the blower intake manifold and the filter.</p><p>The filter uses negative pressure from the blower intake, pulling air from the enclosure. As the enclosure is not air tight, air infiltration helps ensure all air leaving the enclosure is via the filter & blower.</p><p>The intake manifold fits a Wathai 120mm x 32mm High Airflow Blower Centrifugal Fan<br/>( https://www.amazon.com/dp/B08Q3Q2354 ). The listed version comes with a 12v supply & voltage/speed controller. You can run at lower speeds for less noise (& less cfm movement). Two intake manifolds are listed, one with a guard & one without. No guard is needed (or recommended) for use with the filter core.</p><p>The core uses a 7.5x50" strip cut from a 16x50" activated Carbon Filter Charcoal Air Filter Sheet ( https://www.amazon.com/dp/B08TWTQXBS). The rolled sheet is held by the clamps (see pictures). You can use a screw to secure the clamps or a small zip tie. I used the zip tie because it was quick & simple.</p><p>Print two copies of the flange, you will need to orient them so that screw holes line up when installed. The flanges are sized to hold the blower intake manifold & filter core tubes. Secure them on installation by drilling a hole & adding a screw on each (see pictures). I used M3 cap screws and matching nuts, obviously other, similarly scaled, fasteners could be used.</p><p>Placement in the enclosure is a matter of personal preference. I used bottom rear partially because my enclosure has a flip top as well as a door, and the side mount was the easiest for me to access with how I have things arranged in the printer area. Mounted to the back wall would have allowed more front/back space for printer placement, but less left/right.</p><p>The same parts could also be assembled to make a standalone filter within an enclosure space.</p><p>This object was made in Tinkercad. Edit it online <a href="https://www.tinkercad.com/things/fIoucP2yZ6g">https://www.tinkercad.com/things/fIoucP2yZ6g</a></p><h3>Print Settings</h3><p><strong>Rafts:</strong></p><p>No</p><p> </p><p><strong>Supports: </strong></p><p>Yes</p><p><strong>Resolution:</strong></p><p> </p><p>any</p><p> </p><p><strong>Infill: </strong></p><p>20%</p><p><br/><strong>Filament:</strong><br/><br/>any any any <br/> </p><p><strong>Notes: </strong></p><p>Supports are only needed if printing the intake manifold with grill. No other components need support.</p><p>Because the flange/intake and flange/filter slip fit were set close to minimize air leaks, I suggest printing a short portion of the mating surfaces to double check if adjustment is needed for your particular printer. Printing the whole part just to find they don't fit would be frustrating. Just place the parts circle side down & print the first 20mm of each to check fit.</p><p> </p><p>If intake or filter tube are a hair too small, blue painters tape can be used to shim up the fit.</p><p> </p><p> </p><p>Category: 3D Printing</p>
With this file you will be able to print Activated Charcoal Negative Pressure Air Filter with your 3D printer. Click on the button and save the file on your computer to work, edit or customize your design. You can also find more 3D designs for printers on Activated Charcoal Negative Pressure Air Filter.