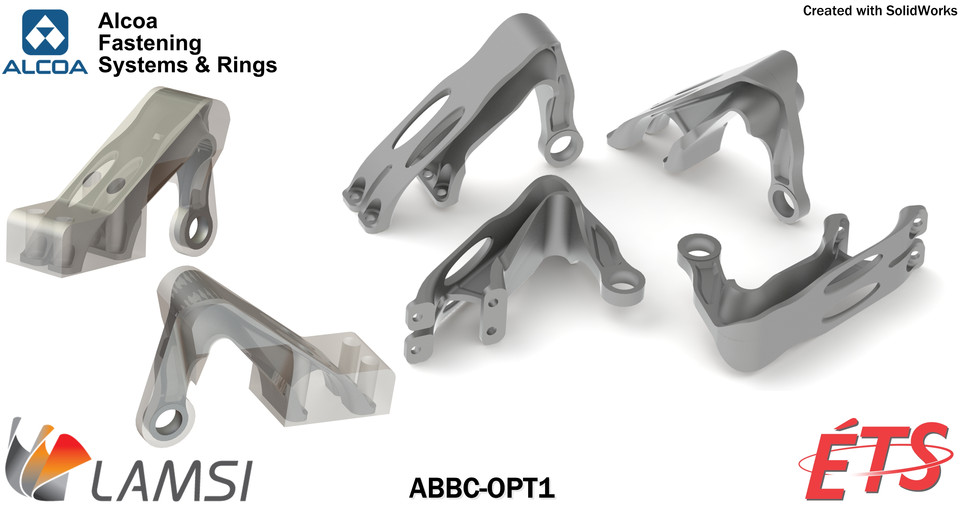
ABBC-OPT1
grabcad
In the Airplane Bearing Bracket Challenge (ABBC), the suggested part design was created through a series of steps. First, a preliminary analysis using ANSYS Workbench R15's finite element method was executed. Next, Solidthinking INSPIRE 2015 was used to evaluate the optimal bracket through topology optimization. The bracket was then designed within SolidWorks. To validate its structural strength, ANSYS Workbench was employed again. Finally, Magics 17 from Materialise generated support structures for the part. The objectives included lowering the mass of the bracket while keeping the Von Mises stress under the yield strength of stainless steel alloy 15-5PH for three load cases. The DFAM paradigm was followed to optimize the design, focusing on reducing the buy-to-fly ratio, using intricate geometries not suitable for conventional manufacturing processes, eliminating tooling and jigs, and lowering lead times. Support structures were minimized to reduce build time and material costs while maintaining part quality. The suggested design's mass was 319.4g, a reduction of almost 63% compared to the original design envelope. Convergence studies using maximum Von Mises Stress for three load cases ensured accuracy in finite element analysis. The promoters and sponsors of the ABBC are acknowledged for their support, as well as the École de technologie supérieure (ETS) engineering school of Montréal and its Laboratoire sur les alliages à mémoire et systèmes intelligents (LAMSI) for access to essential tools and software.
With this file you will be able to print ABBC-OPT1 with your 3D printer. Click on the button and save the file on your computer to work, edit or customize your design. You can also find more 3D designs for printers on ABBC-OPT1.