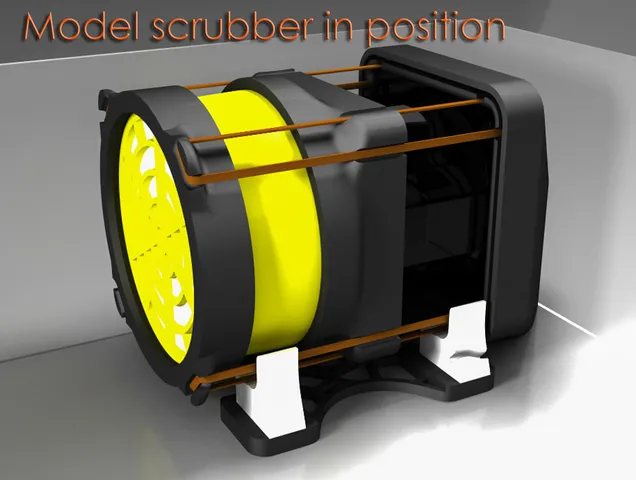
A replicator 2/2X air scrubber that really works..
prusaprinters
ABS printing produces toxic nano-particulates that you do not want in your lungs. (http://www.sciencedirect.com/science/article/pii/S1352231013005086) This compact design works within a fully enclosed Replicator or any Replicator 2 or 2X to scrub the air pretty well. (... but still ventilate your workspace!) It uses a readily available high static pressure fan and air filter and an elegant assembly cum suspension system (rubber bands!) to isolate vibration. It also has a simple exhaust which passes filtered air out of the Replicator case. The base and exhaust have recesses for small high strength magnets to ensure the fan does not move around while in operation. see update notes for important addition and usage information updated September 16, 2013 Instructions DESIGN You do need to be careful of the fumes created by ABS printing. Fortunately the closed space of the Rep2 / 2X printers (or if you have enclosed your 1st generation Replicator) allow for an effective air scrubber. The challenge is to get enough air pressure to get some flow through readily available filters that will actually go some way towards filtering the ABS nano-particulates out of the air. Tubular blower fans are just good enough to do the trick - and to be effective are in any case small. The design places the filter and blower fan together with the absolute minimum of components. Elastic bands provide an elegant assembly approach that both allows simple filter changeover - and suspension for the fan assembly so fan vibrations are not communicated to (and then radiated from) the case.They also isolate the scrubber from the exhaust assembly The support base is very simple - with spaces for small high coercivity magnets to ensure the fan does not move around in the case (and potentially get in the way of the build plate). For fun I used a voronoi strutwork for the base "because I could", having written a Rhino3D/Grasshopper programme that generates these automatically for any arbitrary surface. The support struts are separable - so you can print them a different colour for a bit of bling. The exhaust is in two parts so that, like all the model, it can be printed without supports. It also has insets for three hold-down magnets. It exhausts air down the rear left bottom case hole. You also pass the fan power leads through the same hole. ;-) NON PRINT PARTS All the parts are easily available... Filter:The filter is a standard RC56R gas / vapour respirator cartridge filter. Australian source is http://goo.gl/cmuU3F. Fan:The fan used is an Orion OD6038, 60x60x38mm 12V high static pressure fan. (http://goo.gl/i4XU1o). At $20, this is not the cheapest fan; but a high static pressure fan is needed to pull air through the filter cartridge... The fan also has high quality bearings and at lower power levels will last longer than the printer. The fan is rated at around 1.3A (or 17W). You are unlikely to need to run it at full rated power! Magnets:6x2mm round neodymium magnets available in bulk from your friendly magnet supplier. You will need seven of them. Power / electricals:You will need a 12V power supply with an appropriate power rating - perferably that can be stepped down to lower voltages since it's unlikely you'll want to run the fan at full rated power. And of course some form of switch and wiring connectors to "glue" the whole lot together. I found an old "wall wart" style DC power supply rated at 1A with selectable output voltages. I'm running the fan at between 7 and 9 volt - where it draws less than 400mA (though about 50% more on startup - which is to be expected). If I decide to drive it harder, I will connect it to a more robust power supply and voltage controller which I have on hand - but which is bulkier... Elastic bands... PRINTED PARTS There are design files for the whole device in rhino3D and STEP formats. STL's are provided for the coupler, base and exhaust. For the base and struts, there are two separate STL's so you can print multicolour if that takes your fancy. The STL's all have skirts to prevent print liftoff; they are actually slightly offset from the models so will separate very cleanly. I printed in standard 0.2mm layers for the coupler and exhaust and 0.15mm for the base. No supports are required for any STLs. CONSTRUCTION Elastic bands make the assembly easy. Do not forget to put an isolator rubber bandaround the coupler motor end as well. This is an important part of the noise isolationand the air flow control. (i.e. not a complete seal but good enough). You will need some pressure to insert the magnets into the base. (Designed this way, but perhaps clean the inner rim with a sharp edge to remove the expansion that happens on the first layer print). Make sure you keep the magnets normal to the insertion point or they can jam. The electricals I leave to you - but make sure you have connectors that allow you to separate the motor / scrubber from the power supply. They need to be small enough to fit through the case corner hole, so you can move the scrubber in and out of the case easily. Do ensure you have oriented the fan and power polarity correctly. The fan pulls air through the filter! Neither the filter nor fan will work properly if you get these wrong. USE / CAVEATS This updated design does an excellent job, creating negative pressure within the case that minimises pollution leakage. The exhaust cowl also eliminates the previous air turbulence within the enclosed case, minimising the risk of print liftoff due to uneven air flows across the HBP. I was quite suprised by the airflow; while I cannot measure it, it seems more than adequate... BUT it is possible some small amounts of ABS vapour will still escape. I do find however that I can print in a normally ventilated room with no odour. (In contrast with having to print with an open window beside the printer and still having significant residual odour aka pollution). However, err on the side of caution - and ventilate your workspace well in any case. The elastic band suspension / construction system works really well by the way. If the scrubber assembly touches the base, significant noise is transmitted to the case; the "lacky bands" eliminate this conductive noise completely. A final observation; "ain't modern modelling software / 3D printing amazing?". The real-time rendered images of the model from Rhino3D are very closely matched by the reality delivered through the 3D printer. And parts that should fit together "just do". I remain gob-smacked every time it happens... NOTE ON FIRST UPDATE (Exhaust cowl) In the first version I mentioned the possibility that I may add an exhaust cowl. With a bit of use it was clear the old recycling scrubber model (i.e. no exhaust) created turbulence that disturbed some prints because of temperature fluctuations. I also wanted to see if a "negative pressure" approach could work - and further improve net exterior pollution levels. The exhaust design snapped together like a charm - and also acts to hide the power leads! It also delivers the promised laminar air flows, negative interior case pressure - and lower noise to boot. The smart ones amongst you will also note I have reversed the direction of the filter catridge; got it wrong first time around and it seems it does affect airflow. Oops. UPDATE ON OPTIMISING USE While the design works great, it turns out the holes in the upper corners of the chassis leak vapour at a rate that is noticeable for long print sessions. Check out the plugs (http://www.thingiverse.com/thing:151513) that will prevent this. You might also like to partially block the rear of the cover to maximise the internal negative pressure effect. This combination of tweaks is delivering very satisfactory performance even when the printer is used all day. Indeed, just these passive features significantly reduce vapour exhaust even without the scrubber. So the fan speed required for the scrubber can now be reduced, reducing noise and I suspect improving the filter efficiency and longevity too. You may want to take out the filter and give it a shake every couple of months to reduce filtrant clumping; not sure whether it makes a difference but can't hurt. The design is now in my "nice" category; readily available parts, minimum of print components, no support structures, reasonable aesthetic - and works really, really well. Enjoy. This is now a finished design. Category: 3D Printer Accessories
With this file you will be able to print A replicator 2/2X air scrubber that really works.. with your 3D printer. Click on the button and save the file on your computer to work, edit or customize your design. You can also find more 3D designs for printers on A replicator 2/2X air scrubber that really works...