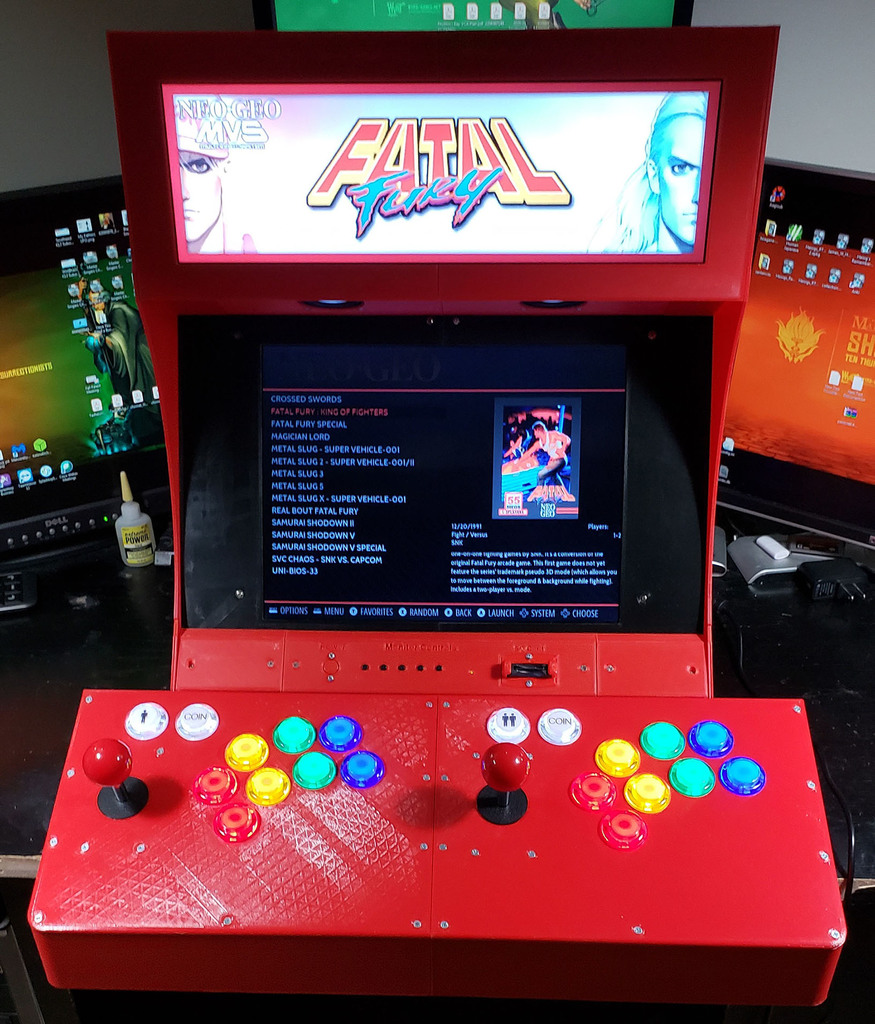
3D Printed 2 Player Arcade Machine
thingiverse
3D Printed Arcade III STEM Project: When I began designing my first printed arcade cabinet, it was my goal to design a couple more at different sizes. This one is the largest with a 14 inch display and 2 player controls. Here are some specs on the latest build. - Designed in Fusion 360 - Printed on two Creality CR-10 minis - Printed using PLA - Five days of printing spread over two weeks - Active marquee - Updates artwork to match game chosen. The Pixelcade LCD marquee also plays GIF animations for select arcade titles. The product is called Pixelcade LCD. Checkout www.pixelcade.org for information on the solutions they offer. - The marquee is ran by a Raspberry Pi Zero W - Powered by a Raspberry Pi 4 B - All components powered by a buck converter regulator system. -Here is a viewable only link to the bill of materials for the internal components and mounting hardware I used. https://docs.google.com/spreadsheets/d/1z_-SHu5X3jC4bZgl-VjIBBc8WmOZwpuI7H0ucnM74FU/edit?usp=sharing -Here is a link to a video demonstrating some of the features. https://www.youtube.com/watch?v=W_9i6rsRqQE -This project started off as something personal. Some individuals became more and more curious and requested access to the STLs. Therefore I am releasing these here as is. I am not an engineer by trade. I am an IT worker with a STEM/STEAM focus for my job. I designed this in the best way I know how. I do not have a lot of time since school has started back up, so revisions will be rare. -I did my best to factor in enough clearance and tolerance for adjoining parts. In some cases a little sanding may be needed to fit parts together. Linear advance will be to your advantage and to help minimize that "bow tie" effect (that's what I call it at least) on the corners of parts. Also use a deburring tool to clean up edges. That will help parts fit better. This is not perfect by any stretch. Certain things could have been designed better, but I can assure you that once everything is assembled it is pretty sturdy. This is not a cheap build so be prepared to spend over 600 US dollars on this if you use the parts I list. I wanted a specific set of gadgets inside of this, so the machine was designed around said list. Please don't ask me to redesign a part. As I mentioned before this comes as is. As I have time I will post revisions that work with the parts list I provided above. -Things to keep in mind: -Disclaimer: If you are not comfortable with soldering or do not have a good understanding of how electronics work together, this project is not for you. If you attempt this build and burn up the buck converters or other components that's on you. I can't and will not claim responsibility for the choices you make or the corners you chose to cut. Take your time. Pretest all of the equipment as a whole before you put it in the cabinet. Create a build plan. -The brackets used to mount the I/O components on the rear of the cabinet and elserwhere were designed around that particular brand and style. You may need to load this into an STL editing tool and make changes if you can't find that brand of part. Amazon has most if not all of the parts on the list from the above link. I will be very specific with the brand I used or link to that component that's provided in the list. -The project will require you to solder things. Use a good solder station, quality flux, and helping hands. -You will need to have access to a multimeter to check continuity on your wiring harness and verify polarity of your power connectors. -You will need to use a multimeter to set the voltage of the buck converters. -I used screw terminal male and female barrel jack connectors for all power inputs. These can handle 16-18 gauge wire. Pre-tin your wire ends as much as possible. -I highly recommend you use the power supply listed in the materials list. It will provide the power system with enough current to drive the components with enough overhead. 24volts with up to 10 amps of current. -I used JST-SM connectors to create a wiring harness. I purchased a crimping tool to properly terminate the wires that fit into the connector ends. I recommend you use the kit I provide or something close to it. This will keep things nice and prevent unwanted shorts. -This is a BIG project to undertake. Plan on a couple weeks and few weekends. Have all of the parts purchased a head of time if you can. You will need a little over 3 rolls of 1K filament spools to print this. Have some spare rolls on hand in case you have failed prints. Some of these parts will use over 1/3 of a 1K spool. Some of these files can take over a day to print. On some of those bigger parts you may want to consider a printing service if you can't afford to tie down your printer for over a day. I have provided a lot pictures to give you an idea of how all of this fits together. Please use them. -Regarding the LCD monitors used for this build: -The main display used was a JaiHo 14 inch 4:3 cctv monitor. I removed the front part of the bezel and trashed it as it was not needed. You will need to carefully open it with a spudger tool and a sturdy guitar pick that comes in most precision screw driver kits. Don't use a screw driver or anything metal for that matter. Take your time with this. Save the buttons on the bottom for the controls. You will cut these from the clip and repurpose them later. -The marquee display is specific to the Pixelcade LCD. You can purchase a kit from pixelcade.org or source your own parts and buy just the software. Please use the links in the bill of materials list to get the correct one.
With this file you will be able to print 3D Printed 2 Player Arcade Machine with your 3D printer. Click on the button and save the file on your computer to work, edit or customize your design. You can also find more 3D designs for printers on 3D Printed 2 Player Arcade Machine .