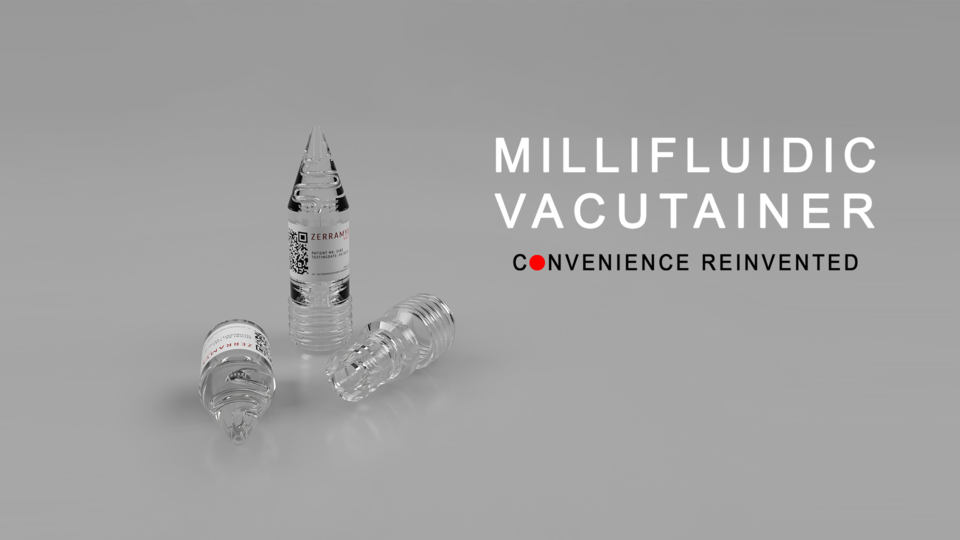
3D Printable Millifluidic Vacutainer
grabcad
This is a solo project by me, a student of the Friedrich-Alexander-Universität Erlangen-Nürnberg. Disclaimer: This is a medical device that's still under development and testing! It shouldn't be used at all for diagnostic procedures - yet. The design aims to overcome the need for invasive blood taking through venipuncture. Puncture of the finger tip with blood lancets and blood capturing with glass capillaries is better than invasive techniques in neonates, patients suffering from obesity or fear of needles, those who are self-testing or elderly with fragile veins. However, the conventional method of capillary blood taking is prone to cause more accidents that can lead to transmission of infectious diseases when handling patients with HIV or HB etc. In contrast to the difficult feasibility when using glass capillaries, the presented design offers an integrated capillary system for blood taking with a capture device for storage, shipping and automatic processing of patient samples that's safe and easy to use. The device was designed to be printed on SLA and DLP machines to sufficiently reproduce the capillary system at 100um layer height. SLA and DLP systems are known to have good accuracy whereas the voxel/staircase effect is lower in SLA machines. DLP machines however tend to produce parts faster when it comes to large amounts because of the all-at-once light exposure of the liquid resin in the resin vat. Biocompatibility is achieved by using biocompatible (additionally sterilizable) resins that fit ISO norms (e.g. EN-ISO 10993-1:2009/AC:2010) and/or approved by national agencies for medical use. Version 1: Transfer of blood from the capillary system is done by inserting the eppendorf tube-like storage system into the capillary device. The total maximum volume of blood that can be captured is close to 1ml. It must be noted that further post-processing of the printed parts is needed by adding a silicone layer onto the storage tube and applying negative pressure to enable transfer of the blood. Despite that, the fully additive manufacturing workflow can easily be achieved when printing a plug with silicone-like or flexible material. A simple boolean operation from the CAD files would create a tight-fitting plug for the storage tube that could be printed contemporaneously. The storage tube is punctured by the needle – which is also printed – in the capillary device. This encased and printed needle ensures safe blood taking without possible injuries as mentioned above. During the design process, a handle with grip was added to the blood storage part to easily detach it from the capillary device after blood transfer. The capillary capture device was designed to have a nose cone shape to easily capture blood drops. Furthermore, a lock-key guide was designed to ensure straight and close-fitting insertion. Positive pressure buildup in the capillary device when inserting the storage device was solved with simple pressure-relieve valves at the top of the capillary device. Visual end-point feedback in the insertion axis is given by the lock-key guide and the convex shape at the tip of the storage handle/bottom of the storage tube. To test the storage tube, a layer of Coltene Affinis silicone was prepared by mixing the base and catalyst in a 1:1 ratio. The mixture was then applied to the storage tube and allowed to cure for 30 minutes. After curing, the storage tube was washed with >99vol% IPA on a magnetic stirrer, microfluidic channels were washed separately, and all devices were post-cured in an UV chamber for 20 minutes. Version 2: The new design approach had in mind to reduce material consumption as well as build volume to print relatively large numbers with less material (e.g. by scaling down the whole design and hollowing some parts like the base of the plunger). On a desktop SLA machine, you can print up to 110 models with 100ml in around 7 hours at 100µm layer height. All parts were printed on a Formlabs Form 2 (SLA) printer at 100um layer height with clear resin. Parts were washed with >99vol% IPA on a magnetic stirrer, microfluidic channels were washed separately, and all devices were post-cured in an UV chamber for 30 minutes.
With this file you will be able to print 3D Printable Millifluidic Vacutainer with your 3D printer. Click on the button and save the file on your computer to work, edit or customize your design. You can also find more 3D designs for printers on 3D Printable Millifluidic Vacutainer.