tormach knife sharpener 3d models
30630 3d models found related to tormach knife sharpener.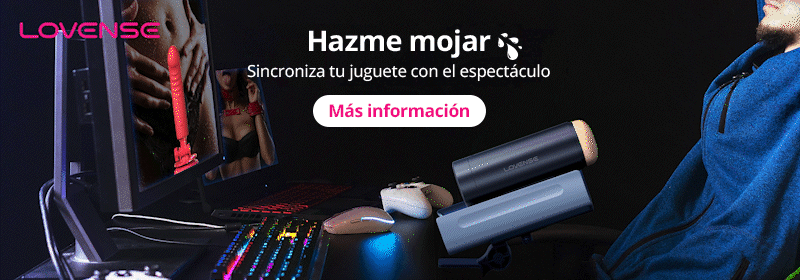
prusaprinters
It's something of a fiddly process. Trim off any brims Clean support material out the threads of the socket Wet-sand the edges of the side and bottom hooks Make sure they fit in the recesses made for them Wet-sand the mating surfaces of the back...
cults3d
Bogie sides require a tight fit to the hub, use a knife to trim the edges if it doesn't fit perfect. If you mount the sides and they don't fit perfect, your wheel shafts will not align and all wheels will not touch the track. The included container...
prusaprinters
With a sharp knife, but a half-inch hole in the middle and remove the magnet. Finally, you'll need to remove the adhesive covering the bolt. Using an allen wrench, remove the center bolt. It's a lot of work. Easier to cut off or grind off the...
thingiverse
If you get the right sizes, the nuts will snap into place and the washers will slide in (sometimes you'll need to trim them with a knife or drill bit or pull them into place with a screw due to the elephant-feet effect). I tried to standardize on...
prusaprinters
Use a file or a knife to make space for the LED legs if you want the LED on. Secure it in place with a drop of super glue. Step 2 Position the buzzer in line with the Arduino. Step 3 Lay/slide the Arduino into the "top" of the shell with the buzzer...
prusaprinters
It is a good idea to scrape the round part of the leg that inserts into the gear lightly with a razor knife. Ideally the leg will fit into the gear firmly but not too tightly. Put each number segment on its respective leg before inserting the leg...
prusaprinters
The wires from each jumper will pass through two notches in the bottom part to reach the slider switches installed on top.Solder the wires to the switches and pay attention to the orientation to match the text on the top part.Display WindowsOptional:...
prusaprinters
On demand, simply punch the according hole out at post-print stage, using a small knife, a screw driver, or a drill of suitable size. Alternatively, you can use TinkerCAD or some other 3D-tool to punch them out digitally at pre-print stage.</p>...
prusaprinters
If you use a knife (per manufacturer instructions), you will produce a much more jagged edge and possibly crack a panel, forcing you to buy another piece - ask me how I know. Place your acrylic panels into the openings and superglue a magnet onto the...
thingiverse
Sainsmart elastic TPU) **Tools needed:** * Drill press * Files * Jigsaw or coping saw * Exacto knife * Soldering iron * Coffee warmer (for warming up hinge plugs) **Step 1-12 Assembly:** 1. \nPre-assemble the finger segments by cutting them to size...
prusaprinters
When the epoxy had set but was not fully hardened I trimmed off the excess with a razor knife. The ironing of the top surfaces worked really well on the test pieces I printed, basically eliminating having to sand around the details on the...
prusaprinters
I ground the blade off an X-acto knife to a square edge to use there. This works pretty well and you end up with a really strong part.</p> <h3> Post-Printing</h3> <p><strong>Trimming supports using square ground X-acto blade</strong></p>...
thingiverse
There are 3 rows of small triangular shaped ribs where the ratchet teeth are that need to be cleaned out with a knife. The teeth should be open and continuous across the width of the spindle. There are a couple of other ribs that need to be cleaned...
thingiverse
The next day use a very sharp knife (xacto is good) to trim the leather flush with the top of the mold. Be VERY careful as it is easy to slip and cut yourself. Ask me how I know. Once it is trimmed unscrew the nut almost all the way but not...
prusaprinters
If you have an elephant foot, you will need to trim it before with an Exacto knife. Slide in the “blockers”, I had a little trouble with it and had to set them in place “gently” with a hammer and a little wood piece (to avoid scratching). ...I've...
prusaprinters
Also, a pair of scissors and Exacto knife may come in handy for trimming the mounting tape. ... The assembly sequence is shown below:Future PlansAmong plans for the future development are:Embed wireless charger into the holder.Improve the rail...
thingiverse
If you use a knife (per manufacturer instructions), you will produce a much more jagged edge and possibly crack a panel, forcing you to buy another piece - ask me how I know. Place your acrylic panels into the openings and superglue a magnet onto the...
prusaprinters
Like… very-nearly-the-whole-MK3s-build-plate-big, so don't be surprisedSettings (how I printed mine, at least):Prusa Slate Silver PETG0.4mm nozzle.2 layer height20% infill (resulted in some surface scarring, but it's not visible on mine when in...
prusaprinters
But if you carefully press the two pieces together all around the circumference they will be joined quite strongly (but can be separated again by prying apart with a knife blade).Torsion - This is the most complicated version, and requires some trial...
thingiverse
Parts Needed: * Suitable 50mm Fan (mine is a YS Tech rated at 11.7cfm; search Amazon for any ball-bearing fan that measures 50mmx50mmx10mm in size and is rated at 12V .08a) * Solder Iron * Solder * Heat Shrink Tubing * Wire Cutters * Wire...
thingiverse
Of course, you could gouge the smaller parts out with a knife and apply liberal amounts of superglue, I've done that during the development process. And you could tap out the holes for the stock if they're too tight and screw threaded rod in. Like I...
myminifactory
(male only)Bionic Pointing, both hand and arm (female only)1 x Winchester Rifle Compatible with Rifle-Stock style attachment joints (also comes stand alone with integrated stock)1 x Rail Rifle Compatible with Rifle-Stock style attachment joints (also...
thingiverse
- Clean up holes with craft knife - Install printed barrel nut on to the M4 upper. Test fit PVC, making sure that the fit is a slip-fit and not press-fit. Sand outside of barrel nut or inside of pipe if necessary. - DO NOT over-tighten the...
thingiverse
can also be used to hold an X-Acto knife! 1-16-18: Added some holes to side of mounting bracket to make it easier to add accessories like sensors, fans, etc. Fixed the mounting holes for fan duct on bowden mount, they were too low. Added locking pin...
prusaprinters
I printed with a 1mm brim to help them stick to the bed, then used a hobby knife to cut the brim off. I used PETG, but I suspect anything would work well enough.</p><p><strong>For the wheel nuts</strong></p><p>Dude, I don't know how I managed to...
thingiverse
XActo Knife or similar blade # Steps **Assemble the main body** First cut the 1x4 wood to sizes: A. 1"x4"x9" B. 1"x4"x2" If you wish, sand the edges and surfaces. Remember to wipe off the dust if you sand it, otherwise your paint/stain won't take...
prusaprinters
A table knife works well.Starting with the lower side mold piece, insert the knife between flanges and pry the flanges apart until remaining silicone gives way.(~5mm). You will feel a clear distinction between the force of the glue and the...
prusaprinters
The wire should be very near to 2.0 mm in diameter.rnrnTools:rn- Screwdriverrn- Utility knife / box cutterrn- 2.0 mm drill bitrn- 2.5 mm drill bitrn- M3 tap Step 1 - Ream Holes for Threads Use the 2.5 mm drill bit to ream the holes that will later be...
thingiverse
Additional items needed: ¼ inch OD brass tubing for the filament cooling air nozzle, M3 screws (you will need to determine lengths yourself—sorry, I didn’t keep track), M3 nuts, CA glue, metal tubing cutter, double sided tape, other tools as needed...
prusaprinters
I used an X-Acto knife to remove it but a drill bit works too. The case screws utilize either self threading into the rear case standoffs or nuts depending on the rear case that is printed. Needed hardware: Case screws for self threading rear case....